

- products
Advanced 260 Vertical Zipper Bag Powder Bag – Making Machine With Intelligent Design
Application:
This packaging machine is highly versatile as it is designed to handle two major types of products. For powder products, it can package items like milk powder, tea powder, spices, and coffee. When it comes to liquid products, it is capable of packaging substances such as honey, milk, oil, ketchup, and juice. It thus provides efficient and flexible packaging solutions that can be applied across diverse industries to meet different packaging requirements.
Suitable Pouch:
It is compatible with a wide variety of pouch types. These include Doypack, Box Pouch, Zipper Pouch, Stand Up Pouch, Stand Up Pouch With Hole, Kraft Paper Bag, and Side Gusset Bag, among others. This broad range of suitable pouches further enhances its flexibility and usability in different packaging scenarios, allowing for customization based on specific product and marketing needs.
Kindly Reminder:
We have experienced team of R & D engineers who can customize packaging solutions according to your product characteristics.
Packing Exambers:
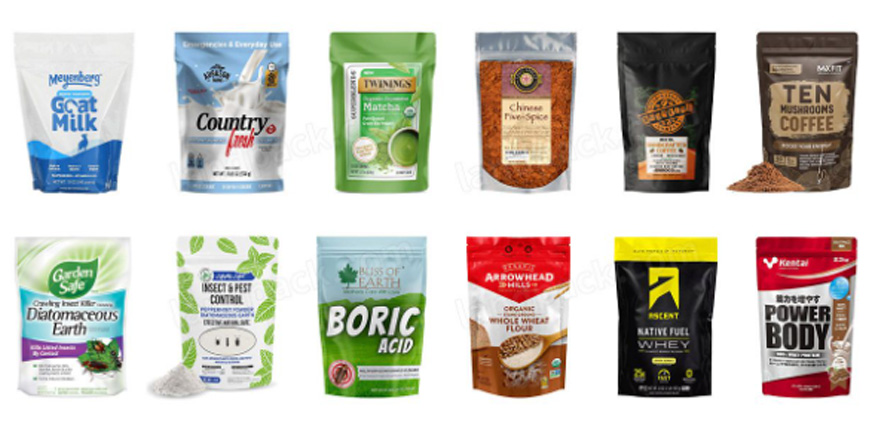
Features
-
Two-in-One Functionality:
The machine has a versatile design that enables it to fill both powder and liquid materials. What’s more, users can easily switch between filling these different materials through the touch screen, providing great convenience and flexibility for handling multiple product types in one packaging setup. -
Horizontal Bag Feeder:
It is equipped with a horizontal bag feeder which plays a crucial role in enhancing the stability of the bag feeding process. This ensures that the whole packaging operation proceeds smoothly without disruptions caused by issues like misaligned or unstable bags. -
Upper and Lower Bag Opening Devices:
These devices are designed to guarantee that the bags are opened completely. By doing so, it creates the necessary conditions for successful and precise filling of the materials, minimizing the risk of spillage or inaccurate amounts being dispensed into the bags. -
Flexible Compatibility:
The machine shows excellent adaptability as it can work with various bag sizes. This characteristic makes it suitable for diverse packaging requirements, whether for small-sized packages for individual use or larger ones for bulk packaging, catering to different market demands. -
User-Friendly Touch Screen:
The touch screen interface simplifies the operation process significantly. With its intuitive controls, operators can quickly learn and master the machine’s functions, which in turn enhances the overall production efficiency, reducing the time needed for setup and operation adjustments. -
Reliable Performance:
It ensures stable and accurate filling operations. This consistent performance is vital for maintaining a high level of packaging quality, enabling the production of uniformly filled packages that meet the required standards time after time.
Workflow
- Auger Screw Conveyor Feeding The Material: The process starts with the auger screw conveyor being responsible for feeding the material. This conveyor mechanism ensures a steady and controlled flow of the material to be packaged, whether it’s powder or liquid, setting the stage for the subsequent steps.
- Bags Feeding: Next, the bags are fed into the machine. This step needs to be carried out smoothly and precisely to align with the subsequent filling and sealing operations, and the horizontal bag feeder mentioned earlier helps to achieve this.
- Date Printing: After the bags are in position, the date printing step takes place. This is an important part of packaging as it allows for clear identification of the production date and other relevant information for product traceability and compliance with regulations.
- Filling Powder 1: Then comes the filling of powder. The machine is designed to accurately dispense the powder into the bags, following the set parameters to ensure the correct amount is filled, which is crucial for product consistency and meeting customer expectations.
- Rotor Pump: The rotor pump comes into play, likely facilitating the transfer and control of the liquid material, preparing it for the next filling step and ensuring a smooth flow of the liquid within the packaging system.
- Filling Liquid 2: Subsequently, the liquid is filled into the bags. Just like with the powder filling, the machine aims to achieve precise and consistent filling of the liquid to complete the product packaging content.
- Sealing: Finally, the bags are sealed. This step seals in the filled powder and liquid, ensuring the integrity of the packaged product and protecting it from external factors such as moisture, air, and contamination during storage and transportation.
Type | DXSP-260 |
---|---|
Bag Type | 3-side, 4-side sealing bag, stand-up bag, handbag, spout bag, zipper bag, compound bag, etc. |
Bag Size | 100-260mm/110- |
Filling Range | 10g-3kg |
Packing Speed | 20-50 bags/min (speed |
Machine weight | 1000KG |
Total Power | 2.0KW |
Work Flow | 1. Giving bag, 2. Pick up the bag(coding), 3. Open the bag up and down, 4. Filing, 5. Heating sealing, 6.Output of product |
Dimensions | 2140*1366*1360mm(L"W*H) |
Collocation | Screw metering, screw elevator |